An Exploration of Terry Towel Manufacturing Process
The manufacturing of towels involves various stages, including spinning, weaving, dyeing, cutting, sewing, and packaging. Each step plays a crucial role in creating a high-quality, durable towel that meets the specific needs and preferences of the customer. From selecting the right raw materials and processing them to the desired specifications, to ensuring quality control and performing post-production inspections, every aspect of the towel-making process requires attention to detail and precision. Whether it’s for personal use or commercial purposes, manufacturing towels requires a complex and intricate process that ultimately results in a product that is both functional and aesthetically pleasing.
תוֹכֶן הָעִניָנִים
1: Towel Factories: Innovating Towel Production Techniques for Improved Quality and Efficiency
Brief Introduction to Towel weaving:
Towel weaving is the process of weaving towels using raw cotton or dyed yarn as raw material.
Towel weaving is divided into plain weave and jacquard weave.
The production of plain weaved towels involves preparing raw yarn into warp beams and weft bobbins, which are directly supplied to towel weaving machines.The fabric produced from the machine is then bleached and processed into various white towels and plain colored towels.
The production of jacquard weaved towels involve dyeing the cotton yarn first and processing it into colored yarns for the warp and weft. The warp yarns are twisted and sized, then made into warp beams through warping, beaming, and denting processes. The weft yarns are wound into bobbins or sent directly to the loom as weft yarn tubes.
Towel looms differ slightly from regular looms, mainly featuring special terry weft-insertion mechanisms and a dual-beam warp-feeding system for both ground and terry warp beams.
If producing towels with satin stripes, a multi-jack device is required;if producing jacquard towels, a jacquard opening device is used; and for producing checked towels, a dobby loom or a multi-color rapier loom is used.
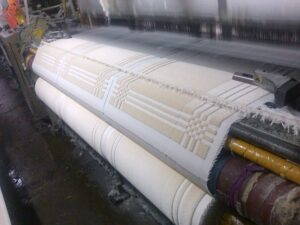
2.The Process of Towel Manufacturing at a Leading Towel Manufacturing Company
1).Process of Clearing Cotton Fibers
Main steps: (1) Loosen the compressed raw fibers into smaller fiber chunks or bundles, facilitating smooth mixing and removal of impurities. (2) Remove most of the impurities, defects, and short fibers that are not suitable for spinning from the raw fibers. (3) Thoroughly and evenly mix fibers from different batches to ensure stable quality of cotton yarn. (4) Roll the fibers into uniform and well-shaped cotton fiber rolls with a certain weight, length, and thickness.
2).Double-carding Cotton Process
Main Steps: (1) Carding: To separate the fibers into single fiber state and improve their straightness and parallelism. (2) Blending: To further mix the fibers evenly. (4) Slivering: To produce cotton sliver that meets the requirements.
3).Combing Process (Third Combing)
Main Steps:Trash Removal: (1)Remove small defects in the fibers.(2)Combing: Further separate the fibers, remove short fibers below a certain length, and improve the length and straightness of the fibers.(3)Drafting: Stretch the cotton sliver to a certain thickness and improve the parallelism and straightness of the fibers.(4)Slivering: Produce cotton slivers that meet the requirements.
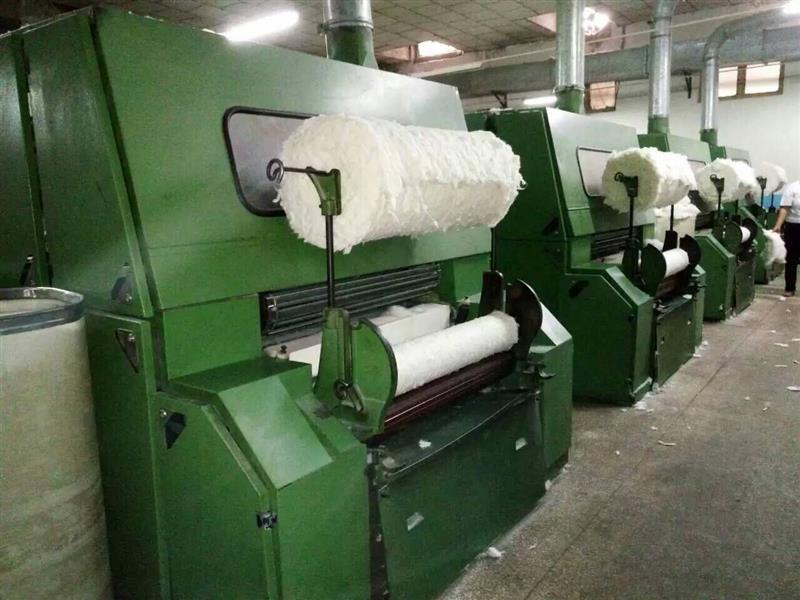
4).Banding Process
Main Steps:(1)Banding: Generally, 6-8 fiber strips are used to band together, improving the unevenness of the cotton strips.(2)Stretching: The fiber strips are stretched and thinned to a predetermined weight, and the parallelism of the fibers is further improved.(3)Mixing: Through banding and stretching, the fibers are further evenly mixed. Different labeled fibers and fibers processed with different techniques are mixed on the banding machine.(4)Banding: Make well-formed loops of mature strips, neatly arranged in the cotton strip bucket, ready for use in subsequent processes.
5).Coarse Yarn
Main steps:(1)Drawing: uniformly stretch and thin the matured yarn, and further straighten and parallelize the fibers.(2)Twisting: properly twist the drawn sliver to give the yarn a certain strength, which is convenient for winding the coarse yarn and unwinding on the fine spinning machine.
6).Fine Yarn Process
Main steps(1)Drawing: stretch the coarse yarn to the required fineness, and straighten and parallelize the fibers.(2)Twisting: twist the sliver to give the yarn a certain twist and strength.(3)Winding: wind the twisted yarn onto a bobbin.(4)Shaping: produce yarn of a certain size and shape for easy transportation and subsequent processing.
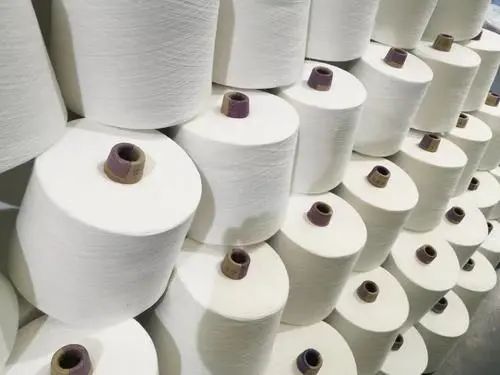
7). Winding
Main steps:(1)Winding and shaping: winding the spool (yarn) into a tube with a large capacity, good shape, and a certain density.(2)Removing impurities: removing some defects and impurities from the yarn to improve the quality of the yarn.
8).Twisting
Main process:(1)Twisting: twisting two or more single yarns together to form a strong and well-structured ply yarn.(2)Winding: winding the twisted ply yarn onto a bobbin.(3)Forming: shaping the yarn into a specific size and shape for easy transportation and further processing in subsequent steps.
9). warping process
The task of warping is to take a certain number and length of warp yarns from the warp beam, and form a warp sheet by guiding them through a series of tensioning devices, so that the warp yarns have uniform tension and are tightly wound in parallel on the warping beam, making it ready for the next process of weaving.
10). Sizing process
To reduce the breakage rate on the loom, the warp yarn needs to go through the sizing process, making the yarn smoother and more robust.
The sizing process involves merging several warp yarns from several warp beams into one sheet, passing it through the sizing solution, and then pressing, drying, and winding it into a warp beam.
After sizing, the sizing solution adheres the protruding fibers on the warp yarn to the warp yarn’s core, increasing the yarn’s smoothness.
At the same time, the sizing solution forms a film on the surface of the warp yarn after drying, which increases the yarn’s abrasion resistance. On the other hand, the sizing solution penetrates into the interior of the warp yarn, bonding some fibers together.
When the yarn is stretched, it can prevent the fibers from moving relative to each other, thereby increasing the strength of the warp yarn.
11). Warp Threading Process
Warp threading, commonly known as warp beaming, is the final process in warp preparation.
The task of warp threading is to thread the warp yarns from the warp beam through the lease rods, heddles, and reed according to the fabric requirements, in order to form a shed for the weft yarn to pass through during weaving and to prevent weaving defects caused by warp yarn breakage.
12). Weaving
Weaving is an important process in a textile factory. The task of weaving is to interlace the prepared warp yarns and weft yarns on a weaving machine according to the specifications and requirements of the fabric, following a certain process design, to produce the desired woven fabric.
13). Fabric Dyeing Process
Main steps:(1)Remove the impurities in the stained area of the grey fabric during the singeing process by simple boiling, and ensure better color absorption uniformity of the grey fabric.(2)Dye the grey fabric using eco-friendly reactive dyes to achieve the desired color required by the customer.(3)Conduct post-dyeing water washing to ensure the grey fabric meets the neutralization requirements when it comes out of the dyeing tank.
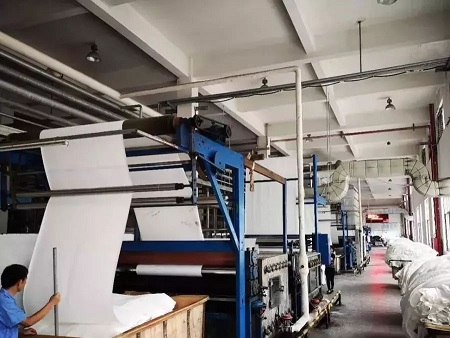
14).Towel Finishing Process
(1)Cut and classify the dyed towels after they are finished.
(2)Sew the towels according to customer requirements, including regular edges, three-needle five-thread edges, double-needle edges, etc.
(3)Inspect the sewn towels, mainly to trim the thread ends during the sewing process, and classify them according to quality level. Transfer first-class products to the packaging process, second-class products and those requiring repair to the repair process for repair.
(4)The main task of the repair process is to repair the towels that can be repaired, and transfer those that can reach first-class quality to the packaging process. Products that do not meet standards are classified and packaged with an indication of their quality level (second or third class).
(5)The packaging process is responsible for packaging the goods according to customer requirements, until the final loading and storage in the warehouse.
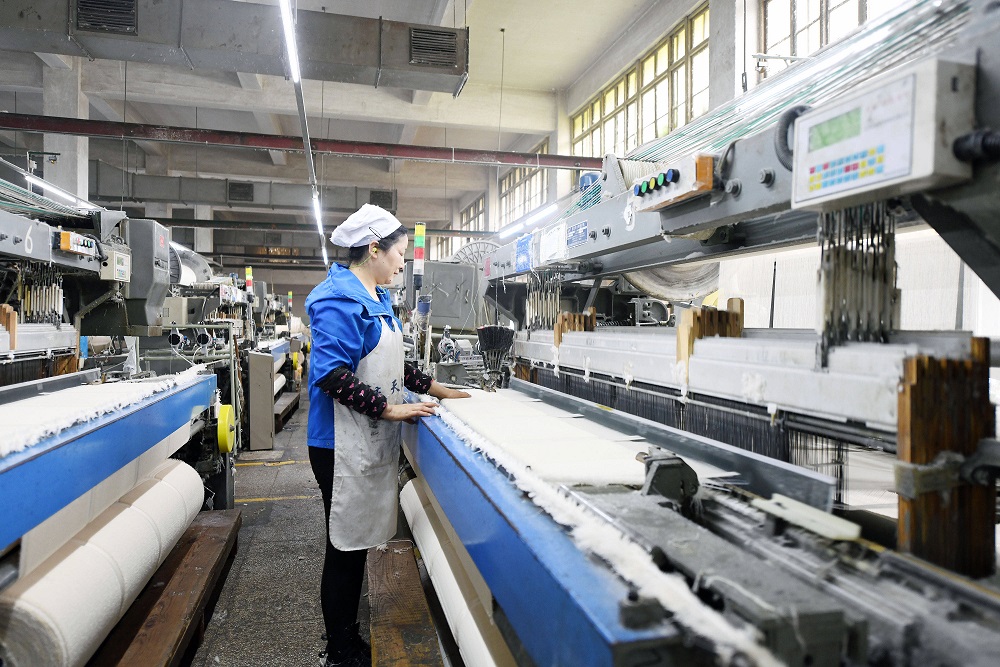
3.Conclusion
In conclusion, the towel production process involves various stages such as weaving, dyeing,cutting,sewing,inspecting and packaging to ensure that only high-quality products reach the market. With attention to detail and careful execution, the towel production process can result in soft, absorbent, and durable towels that provide comfort and functionality to consumers.Therefore, it is crucial to choose a reputable towel manufacturer that uses quality materials and employs skilled workers to produce towels that meet customer expectations.